Gartner predicts that through 2023, less than 5% of control-tower-like deployments will fulfil their end-to-end potential due to mindset and cultural obstacles. On a positive note, IDC predicts by the end of 2024, 40% of Asian-based supply chain organisations will have rebalanced resiliency efforts to reflect the realities of inflation and necessary efficiency to recover two percentage points of margin.
Better still, by 2026, IDC predicts that 45% of Asian-based organisations will operationalize integrated sustainability in the supply chain, enabling a 10% waste reduction.
So, are you a half-full or half-empty leader? We spoke to two industry observers for their take on the challenges and opportunities for organisations transitioning through their supply chain modernisation effort.
According to Stephanie Krishnan, AVP of the Manufacturing and Energy Insights Program at IDC Asia/Pacific, Asia-Pacific supply chain participants face market challenges such as escalating supply costs, demand volatility, and supply chain execution issues. These challenges make it hard for them to adopt new tools for supply chain planning.
In IDC's Future Enterprise Resiliency Survey (Aug 2023), 40% of respondents from Asia-Pacific manufacturing, logistics, and retail organisations indicated that a possible recession in 2023 would reduce specific IT spending items for the rest of 2023. Another 40% indicated that this would affect 2024 budgets.
Krishnan believes that at the organisational level, resistance to embracing supply chain technologies and modernization exists for various reasons.
Lack of understanding: Often, organisations resist new technologies due to a lack of knowledge about how these technologies work and how they can benefit the supply chain. This resistance may arise from a fear of the unknown and a reluctance to change established processes.
Cost concerns: Concerns over the costs of implementing these technologies can deter organisations, as they worry that the expenses may outweigh the advantages.
Fear of disruption: Implementing new technologies can disrupt existing workflows and processes and may negatively impact day-to-day operations.
Regulatory and compliance issues: In some cases, the complexities of integrating new technologies into existing systems contribute to this resistance as organisations lack resources or are unclear on navigating compliance pathways.
Unclear technology benefits: If organisations cannot see how supply chain technologies will improve their performance or competitiveness, they may hesitate to invest in them.
Strategy alignment: Technology selection is not aligned with the overall organisational strategy, and reluctance to invest may persist.
Kuntha Chelvanathan, partner and APAC Supply Chain and Procurement Transformation leader at IBM Consulting added that traditionally, supply chain professionals have had their tools and methods.
“Naturally, when introducing new tools, there would be resistance to change as supply chain practitioners are still unfamiliar with the technology as well as the data models, algorithms or simulations involved,” she added.
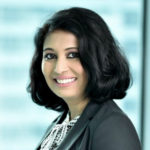
“People need time to learn about how the accuracy of the new demand forecasts work and what factors they take into account. There is also a need to finetune and drive the best outcomes by making it easy to compare the insights from a new tool with traditional forecasting methods to ensure the adoption and buy-in to the new system and methods.”
Kuntha Chelvanathan
Is simplification the way forward?
Resistance to change remains the biggest obstacle to organisations’ efforts to modernise or digitalise their supply chain.
IDC’s Krishnan observed that there has been a significant shift in the supply chain technology landscape. The focus is now on striking a balance between user-friendliness and robust functionality. She added that this change is partly attributed to the entry of the next generation of employees into the workforce.
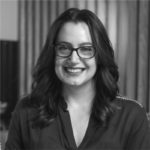
“These young professionals grew up in an era where sleek and user-friendly interfaces were the norm in consumer technology. As they transition into professional settings, they bring high expectations for technology usability. Moreover, young graduates are introduced to more sophisticated technology through universities and colleges and are entering planning environments often dominated by Excel.”
Stephanie Krishnan
She cautioned that the contrast can significantly challenge the efficient adoption and utilization of complex and non-intuitive supply chain technologies.
She also warned that in Asia, companies face a problem known as "ghosting," which occurs when employees become disengaged or lose motivation due to outdated and complex technology use in organisations within the supply chain.
“Lower productivity, increased mistakes, and higher employee turnover can result, all of which can hurt a company's success. In talking to technology buyers, we have noticed a growing trend for simpler and more efficient interfaces,” she recalled.
This trend includes custom features that allow users to personalize data entry and viewing screens to suit their needs and preferences, ultimately improving their experience and productivity in the supply chain environment.
Training to drive adoption
IBM’s Chelvanathan says “One way is to embed supply chain practitioners into the design and development of the system during the implementation and another key area is to embed feedback from the team in the system.
“This brings about two benefits: getting buy-in on the new tool and helping to train supply chain professionals on the job,” she added. “Constant finetuning and collaboration are essential to drive higher adoption rates while providing supply chain professionals with a more comprehensive view of supply chain KPIs.”
According to IDC's 2023 Future of Work Survey, hybrid learning (in-person and digital) and digital adoption platforms for manufacturing, retail, and transportation organisations are the top two initiatives that have been undertaken to improve skilling generally.
Krishnan says to drive higher technology adoption rates, training and education strategies should evolve to encompass several key aspects beyond merely addressing initial feedback and concerns:
Continuous learning culture: Organisations should foster a culture of continuous learning. This involves not viewing training as a one-time event but as an ongoing process. Regular updates, refresher courses, and access to resources should be provided to keep employees current with the latest technology developments.
In Situ application support: The offering of real-time support and instruction while employees actively use the technology is becoming crucial. On-demand chat support (trending towards generative AI to assist in this context) and text and video tutorials can guide the work process.
Gamification and interactive learning: Incorporating gamification and interactive learning elements can make training more engaging and effective. This approach can include quizzes, simulations, and competitive aspects that motivate employees to participate in the learning process actively.
Accessibility and inclusivity: Ensure training materials and methods are accessible to all employees, including those with disabilities, to ensure inclusivity and prevent anyone from being left behind during adoption.
Peer learning and knowledge sharing: Encourage peer learning and knowledge sharing among employees, which includes mentorship programs, internal communities of practice, and forums where employees can exchange tips and insights related to technology usage.
Measuring adoption success
Supply chains will likely be familiar with the supply chain operations reference (SCOR) model – a management tool used to address, improve, and communicate supply chain management decisions within a company and with suppliers and customers of a company.
IBM’s Chelvanathan suggests looking into the extent of supply chain components that can be automated versus manual. Whilst they now have more access to visibility across the supply chain and the key Supply Chain KPIs, this can be used to measure and monitor their supply chain performance over time. A control tower-type visibility can give them a good view to look at the before and after impacts of their tools.
For her part, Krishnan says gauging how well employees and stakeholders adapt to new technologies is essential. She suggests evaluating their satisfaction with the technology's usability, functionality, and overall experience. Frequent feedback surveys and interviews can be helpful for this purpose, she noted.
Some measures can be collected through technology that can also be useful. These include daily, weekly, or monthly active users (DAUs, WAUs, and MAUs), frequency of usage, failed tasks, task completion rates, and application engagement rates.
Krishnan says assessing overall productivity is an example of a critical success metric that often closely aligns with business outcomes. She opined that organisations could determine the impact of an application on employees' productivity and output levels by monitoring efficiency gains, task completion times, and workload reduction.
“Ultimately, measuring the impact on efficiency (or quality, etc.) is a vital way for organisations to measure success, as technology is only adopted to achieve specific outcomes,” she concluded.