In 2022, Frost & Sullivan estimates that Asia-Pacific contributes to nearly 48.5% of the global manufacturing output. The analyst says more countries in the region are developing advanced manufacturing capabilities to grow Industry 4.0. These emerging technologies also play a crucial role in helping us achieve our decarbonisation goals, as sustainability becomes a core priority in business operations.
But what other factors are reshaping the region’s manufacturing sector?
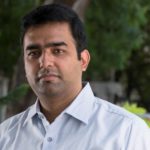
According to Frost & Sullivan senior analyst for industrial, Ram Ravi, the COVID pandemic has caused considerable disruption to the global supply chain.
“In a bid to develop supply chain resilience, organisations are diversifying their supplier portfolio and moving them closer to end markets. This trend positively impacts more manufacturing investments in the region, as ASEAN countries are among the fast-growing economies globally,” he continued.
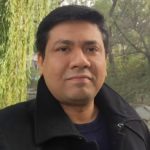
Shivaji Bose, head of the manufacturing business unit at Tata Consultancy Services (TCS) Asia-Pacific says this could see close to seven per cent of employees (21 million) could lose their jobs during the pandemic.
On the bright side, he pointed out that the pandemic has spurred demand in healthcare, e-commerce, and other digital fields and provided opportunities for displaced labour.
“We believe that many of the 100 million new jobs to be added by Industry 4.0 will be in Asia and ASEAN; facilitating reskilling and redeployment at scale will be a key focus,” he opined.
According to IDC’s Asia/Pacific Manufacturing Insights annual survey 2021, manufacturing organisations in ASEAN have been challenged with concerns around declining sales, demand variability and increased competition.
The focus has been around enabling organisations that can counter the shrinking margins through product innovation and new revenue stream identifications that are not restricted to after-market sales and services.
Tech in Industry 4.0 to the rescue
IDC’s Future Enterprise Readiness Survey (FERS) 2022 revealed that over 82% of the Asia/Pacific manufacturers have either adopted or planning to adopt a ‘digital-first’ strategy to counter the effects of market disruptions.
The biggest benefit of Industry 4.0 drive has been its ability to enable visibility across all the value chain processes and operations. Enhanced visibility in turn would aid in providing fail-safes and contingencies that can address unscheduled downtimes and disruptions.
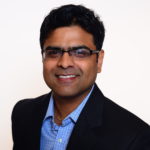
Sampath Kumar Venkataswamy, senior research manager for IDC Manufacturing Insights says that to make the whole process as seamless as possible there are 4 main data segments that organisations need to invest in storage, analysis and computing, visualisation, and remote monitoring and digital twins.
“The degree of adoption is understandably lower in countries such as Myanmar and Cambodia when compared to some of the more industrialised neighbours due to the availability and readiness of workforce who are willing to work at lower wage points.,” he continued.
IBM claims that the average factory generates more than one terabyte of production data daily, but only one per cent is analysed and acted upon in real-time or being used for decision-making.
Srinivasan Chary, practice leader for edge, manufacturing optimisation services at IBM, says technology investment is dependent on the nature of manufacturing complexity, overall process maturity in the specific sub-industry, and related criteria.
“The priorities for Industry 4.0 investment appear to be varying. However, these are only the point of inflexions of these respective Industries, as per the most viable roadmap respectively, the ultimate end state each manufacturer is moving towards is common, and that is to achieve a mature Industry 4.0 System at the end of the journey,” he continued.
Core competencies
Asked what core competencies manufacturers must exhibit to benefit from the innovations that Industry 4.0 promises, Bose called out the ability to create exponential value by adding products to a base transaction. “Companies are adding not just more products but also services to create value, customer centricity, and services innovation at scale,” he added.
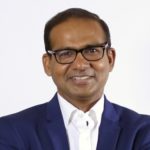
Chary cautioned that the story does not end with the successful implementation of Industry 4.0 enabling systems. For any manufacturer to benefit from these systems, there are some fundamental shifts to be made in the way of working.
He cited agility as one explaining that globally, the factors impacting a business are changing rapidly, and any manufacturer today needs to wear an “agile” hat in running the planning, scheduling, operations, and maintenance. “Industry 4.0 systems assist a manufacturer to respond much faster to a particular change, be it environmental, regulatory, ecosystem driven,” he opined.
The other involves the upskilling and reskilling of talent. He reasoned that enabling the in-house workforce to adapt to the new ways of working ushered in by the Industry 4.0 interventions, as well as bringing in fresh skills needed to perform new roles generated by the same, is paramount.
“Any workforce carries valuable knowledge of the business operations and making sure they are upskilled to perform better leveraging the new systems will be key for continuity. As manufacturing plant construct shifts to add more technology-enabled components, there is also the need to bring in fresh talent to manage the new parts,” he concluded.
For his part, IDC’s Venkataswamy says increased availability of data would mean that there is a need for a governance mechanism that dictates who and how the data gets owned.
“Bearing in mind, that the success of any business model innovation is built on integrated and comprehensive data visibility, several manufacturers struggle to get an acceptable framework that integrates the shop floor with the top floor in place.
IDC’s FERS 2022 revealed that 43% of the APAC manufacturers believe there is a lack of executive alignment about digital infrastructure resiliency and digital business priorities. Organisations need to invest in efforts to sell a technology-led innovation and digital transformation (DX) idea by emphasising the quality benefits instead of focusing on productivity gains alone.
“Often, the core intentions of a digitalisation drive get masked by the cost reduction or organisational re-jigs resulting in resistance within. The buy-in needs to happen from top-down and the executive committee consisting of CEO, COO, CFO, or the CIO needs to be the key stakeholders,” said Venkataswamy.
Finally, he commented that despite the existing competition, organisations need to look to focus on either creating or participating in industry forums that could aid in establishing best operational practices across the various manufacturing processes.
“For instance, industry cloud solutions could drastically reduce the procurement and sourcing timelines and would allow organisations to launch innovative processes to further streamline their existing operational playbooks,” he concluded.