While some manufacturers are still depending on manual labour to meet manufacturing needs, Universal Robots (UR) share the benefits of automating through collaborative robots or cobots.
“Adopting industrial robots is like jumping the deep end of a pool of automation while continuing manual labour is equivalent to wading in the shallow end. Collaborative robots (cobots) are a very manageable option for manufacturers looking to jump into automation, giving them incremental ways of automating,” said Adam Sobieski, regional president of Asia Pacific at Universal Robots (UR).
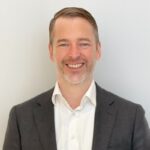
Benefits of cobots
1. Flexibility. One of the benefits of deploying a cobot instead of investing heavily in a conventional industrial robot is its flexibility. Cobots can be relocated and reassigned to perform different tasks.
2. Safety. Cobots are designed to work closely with human operators unlike big industrial robots that require multiple safety measures
3. Simple. Cobots are simpler to operate, easier to set up, and easier to learn.
Adoption reservations
McKinsey & Company reports that automation has the potential to increase global productivity growth by 0.8% to 1.4% annually. However, despite its growth and benefits, the manufacturing industry still has reservations about integrating cobots into their factory lines.
As an example, Malaysia’s robot density per 10,000 employees is still below the global average despite the manufacturing industry’s 24% contribution to Malaysia’s GDP. This indicates a less-than-ideal automation adoption in the industrial/manufacturing industry.