Increasing competitive pressures, tight labour markets and growing environmental compliance objectives require companies to adopt a more holistic management approach that spans the product and asset lifecycle.
Expanding their long-term partnership, Siemens and IBM will develop a combined software solution integrating their respective offerings for systems engineering, service lifecycle management and asset management.
The combined software solution will optimize product lifecycles. It will also enable companies to improve traceability across processes, prototype and test concepts much earlier in development, and adopt more sustainable product designs. The goal is speed innovation up and time to market which can lead to improved quality and lowered costs.
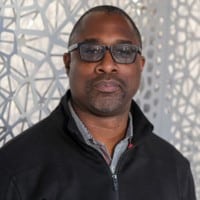
“A significant portion of product innovation and differentiation contains electrical, electronics and software components. Yet, manufacturing companies are struggling to bring new products to market on time, as the current tools, processes, and information to manage these components are siloed and disconnected,” said Kareem Yusuf, senior vice president of product management and growth at IBM.
“To address this gap, IBM and Siemens are collaborating on a digital thread environment to integrate sustainability practices throughout the lifecycle of a product, from design, production, operation, maintenance and beyond. This connectivity will help enable quicker time to innovation and compliance preparedness, and overall improved product quality.”
Kareem Yusuf, IBM
Inside the combined software solution
The new combined SysML v1 standards-based suite of integrated engineering software is expected to support traceability and sustainable product development using a digital thread that links mechanical, electronics, electrical engineering and software design and implementation.
It is intended to span the product lifecycle, from early design and manufacturing to operations, maintenance, update and end of life management.
Initially, the companies are working to connect IBM Engineering System Design Rhapsody for systems engineering with solutions from the Siemens Xcelerator portfolio of software and services including Siemens’ Teamcenter software for Product Lifecycle Management (PLM) and Capital software for electrical/electronic (E/E) systems development and software implementation.
The companies have also connected the IBM Maximo Application Suite for asset management with Siemens’ Teamcenter software to support an integrated digital thread between service engineering, asset management and services execution.
These integrations will focus on the effective reuse of processes and materials to allow traceability for sustainable product development.
This can help companies to make informed decisions earlier in the design and engineering process to help drive improvements in cost, performance and sustainability.
For example, companies can more quickly identify under-performing components or design elements that consume excessive amounts of power, or require maintenance or early replacement, and product innovation can be driven through an integrated digital thread that connects the physical and software assets back into product development.
Kamil Mrva, chief information officer at ŠKODA Group and early adopter of the service lifecycle and asset management solution, said: “We are working very closely together with Siemens and IBM to help us to reach our sustainability goals, reduce total cost of ownership (TCO) of products for our customers and support our business transformation with an increased focus on services.”
ŠKODA Group focuses on railway equipment manufacturing and is a leading European manufacturer of vehicles for railways and public transport.
Another combined solution in the pipeline
Siemens and IBM are also collaborating to create a SysML v2 based solution with a migration path to help customers transition to next-generation systems engineering.
SysML supports the specification, analysis, design, verification and validation of a broad range of systems and systems-of-systems. Service lifecycle management can assist in maximising business value for product servitisation by connecting service engineering to service maintenance to facilitate new collaborative processes between OEM and operators.
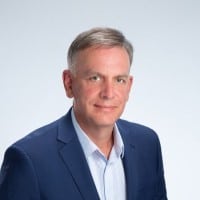
“Together, Siemens and IBM will deliver a simulation-driven systems and software engineering solution that is designed to cover the full operational lifecycle. This can empower our customers to innovate by helping to reduce product development costs, drive continuous improvement and create operational efficiencies across the extended enterprise throughout the product’s operation lifecycle,” said Tony Hemmelgarn, president and CEO, Siemens Digital Industries Software.
“We are developing this to help companies truly shift left by improving extensibility and reuse of systems models and associated data with standards-based solutions in an open ecosystem and to enable our customers to develop better products.”
Tony Hemmelgarn, Siemens Digital Industries Software
Siemens will be supported by benefits through IBM's newly launched Partner Plus program and will offer the solution as part of the Siemens Xcelerator ecosystem.