Most supply chains are built around cost-effective and reliability KPIs.
Changes in customer behaviour, calls for more personalized products and immediate, inexpensive delivery have clashed with supply chain mantras of dependable supply at the lowest cost. Rising trade tensions, market shocks, disruptive technologies and the increasingly severe effects of climate change, have all further eroded supply chain reliability. A prolonged and unpredictable event like the COVID-19 pandemic has made the failings of the supply chain even more acute and finally visible to persons outside the supply chain ecosystem.
The KPIs of cost-effective and reliable delivery are now proven ineffective in the COVID-19 scenario.
The response
Supply chain leaders are now mandating resilience and sustainable strategies to stay business-as-usual.
Making this resilience a reality, however, requires executives to have visibility into how materials and goods enter and move through the chain, as well as the ability to trace inputs and outputs all the way to the hands of the customer.
A new research from Bain & Company and World Economic Forum, Visibility and Traceability: The Twin Engines of Sustainable Supply Chains, finds that fewer than 15% of executives feel their current capabilities allow them to deliver consistent traceability.
“The coronavirus pandemic highlighted the obvious dangers to a business whose supply chain cannot operate in a crisis and made it clear that resilience has become as important as reliability and efficiency,” said Hernan Saenz, global head of Bain & Company’s Performance Improvement practice and co-author of the report.
He noted that resilience comes with huge benefits for companies that can continue serving their customers and to meet their increasingly changeable demands.
“Similarly, companies that lack sustainability will find their products penalized by regulators and scorned by customers, while companies that can point to sustainable practices and products will be rewarded,” he added.
Meeting growing demands from stakeholders for sustainable supply chains means executives must have a view into what is happening across their supply chain and the ability to trace items as they travel from field to factory to customer (and beyond).
“Today, the technology exists to turn this need into an operational reality, but companies must still figure out how to harvest and share data, which technologies to adopt for their priority business cases, and how to best deploy external certifications,” added Juliane Stephan, associate partner in Bain & Company’s Performance Improvement and Digital Transformation practices.
Companies have started to build some capabilities, but most give their efforts low marks for sophistication as they struggle to scale them, integrate them or realize business value. Unreliable or nonstandard data top their list of common barriers to traceability, with technical and organizational barriers close behind (see below).
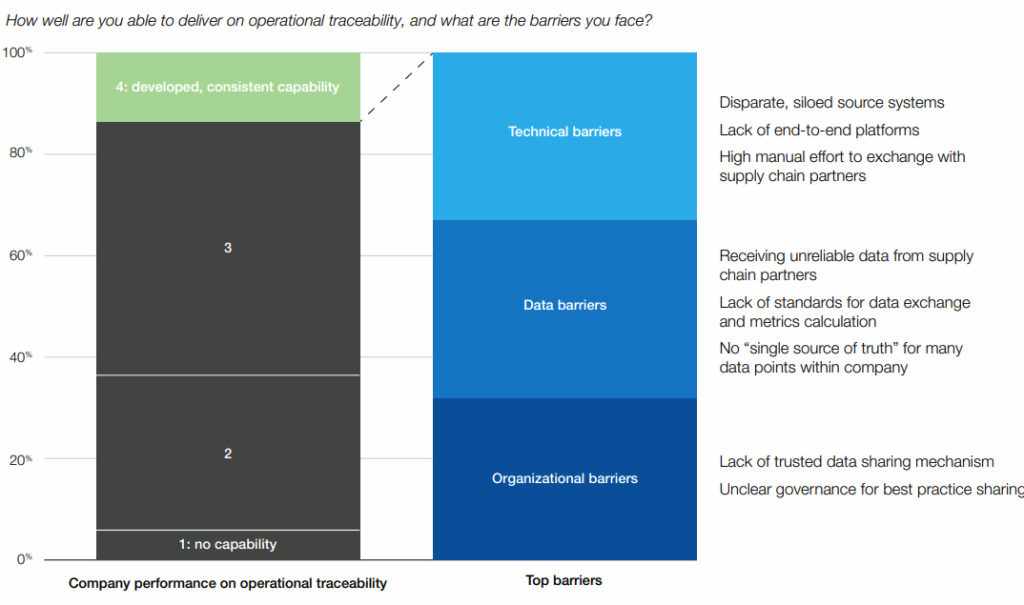
Four step in the journey toward traceable supply chains
The joint report found that the journey toward traceable supply chains involves four key steps for companies:
Carefully defining how visibility and traceability will provide value. To produce the greatest benefits, companies should pursue visibility and traceability approaches that are closely tied to their business and customer strategy.
Mapping out the data model and collecting the necessary data across the supply chain. Despite vast amounts of siloed, partially structured data, companies often still find the data they need doesn’t exist in internal systems—or isn’t available at all. They must learn how to integrate external data sources, including logistics systems and suppliers’ ERPs, and how to begin collecting critical data that is not available today.
Assembling a next-generation technology stack to facilitate data collection, analysis and sharing. When evaluating the market, companies should consider how these new systems will fit into their current systems landscape. Some systems will primarily serve as source for required data while others will be the enablers for aggregation, analysis, and sharing.
Implementing the right data operating model both inside and outside the company. Effective data sharing starts inside each company by overcoming silos to create a single source of truth for relevant data. Companies need processes, systems and talent for data collection, cleansing, and analysis to turn data into insights that can fuel business decisions. Only then can they figure out the right way to share the data with ecosystem partners. Companies also need to consider who owns the shared data and the resulting analyses and figure out how to ensure strict privacy for the source data.
Few companies can build visibility and traceability into their supply chains on their own. Instead, the effort requires collaboration among multiple stakeholders within a sector, both to set standards and fund platform-type investments and to focus resources, share costs, and gain traction.
If multiple players in a sector align on a common language, standards, and data model, all will benefit from accelerated capability development, less decision complexity, easier benchmarking and collaboration.
“Our view is that industry leaders—moving ahead of regulators – will likely push the initial development of the platforms and set the standards, and then will be joined by other industry players who see the value,” said Tessa Bysong, Bain & Company partner and World Economic Forum Platform fellow.
She cautioned that the companies that take the lead in collaboration today will have the advantage. Those that sit on the sidelines will have to be content with whatever the industry ultimately adopts.