Despite all the advances in technology and the innovations it has enabled, enterprises remain vulnerable to unpredictable forces.
It’s hard not to be distracted by the daily news about wars, fuel shortages, health crises, and how all of these are impacting daily lives by way of disruption to the supply chain. Gartner says, “supply chain disruption is no longer an “if”, nor is it a “when” since it’s both omnipresent and unpredictable at the same time.
“The question you must answer is: Are we able to mitigate the next global supply chain disruption that comes our way?”
Gartner
Agility and resiliency aspirations
IDC says enterprise agility and operational effectiveness depend on the responsiveness, scalability, and resiliency of the digital infrastructure used to enable mission-critical applications, data operations, and connectivity demanded by customers, partners, and employees.
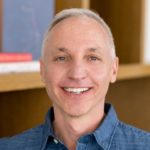
John Lipsey, sr. vice president for brand & corporate marketing at Kofax wrote that “true resiliency and agility requires organisations to embrace the latest innovations in digital workflow transformation and apply intelligent automation (IA) strategically to business processes and workflows.”
But is having automation alone sufficient to achieve resilience and agility? Wouldn’t optimisation be the better starting point for any effort at improving operational agility and resiliency?
“Historically, automation meant creating rigid applications for business processes such as claims or purchasing. These have since evolved into automation of more complex tasks involving interaction and integration with more than one system and product,” said Adrian Bugaian, delivery partner at Endava.
Giap Bui Dinh, head of hyperautomation at FPT Software, clarifies that process automation combines software tools, people, and processes that streamline a system to improve quality, minimise costs, and simplify the business process.
In what way is optimisation a pathway to automation?
Adrian Bugaian: Most processes are completed by various stakeholders across the value chain. Optimising the various workflows means first identifying problems and discussing steps to take for improvement. This then opens up new conversations around tools that can help improve efficiency, including the introduction of automation to free employees from mundane tasks and for more value-added work.
Giap Bui Dinh: There are multiple ways to optimise processes before automation. We recommend applying process or task mining as the ultimate option to continuously explore the processes and discover exactly where automation can deliver the best value.
You can automate without optimising a process? In what condition is this possible?
Adrian Bugaian: It is possible to automate without optimising first, but that process could end up causing problems long-term if it is not optimised for success from the get-go.
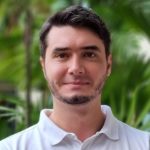
“Organisations facing a labour shortage, for example, might have no choice but to automate simple processes such as bookkeeping and data entry so that employees can focus on more business-critical tasks.”
Adrian Bugaian
Giap Bui Dinh: With IA, businesses can automate smartly without optimising process awareness and optimisation because this technology automatically identifies process flows, finds and fixes missing or incorrect data, enables process documentation, and suggests and makes modifications to processes to improve overall flow.
Can an organisation optimise, skip automation, and still proceed with digital transformation?
Adrian Bugaian: To do so would be counterproductive and can slow down any digital acceleration efforts, which in turn prevents companies from reaching their target goals. We are in the age of digital necessity, and organisations must be able to respond rapidly to customers who now want information and services on-demand.
Aside from agility and real-time insights, automation also allows for reduced time to market, increased scalability and transparency of operations, and improved reliability of processes - all vital requirements for the success of modern digital enterprises.
Giap Bui Dinh: No. Digital transformation is essentially the use of technology to radically change the business by pursuing new revenue streams and business models while avoiding disruption. It means that digital transformation is leveraging all the digital tools, including automation and data analytics capabilities to fundamentally transform business practices. Therefore, automation plays an important role in the pathway to digital transformation.
How does AI/machine learning support optimisation?
Adrian Bugaian: When optimisation is first rolled out, the requirements on what processes and workflows need to be relooked at are input by people. Machine learning (ML) helps to take optimisation forward with its ability to learn from previous experiences. Unlike people, ML algorithms can analyse vast amounts of historical data and provide relevant insights for better business decisions.
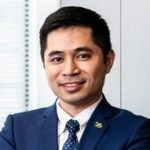
Giap Bui Dinh: AI and ML bring data-driven intelligence to DevOps, a set of tools and practices designed to increase organisational ability to deliver applications and services faster than traditional software development processes.
“AI-driven optimisation can eliminate errors in optimisation processes by identifying important patterns, proactively preventing difficulties, quickly detecting and resolving problems, and enabling staff to make optimal and fact-driven decisions.”
Giap Bui Dinh
ML involves using an algorithm to learn and generalise from historical data to make predictions on new data. It helps businesses to minimise error, cost, and loss of data.
What would a strategy that brings together AI, optimisation and automation look like where the goal is to achieve the maximum potential of all three ideas?
Adrian Bugaian: It is now clear that these ideas are interdependent. The optimal strategy is to have optimisation as the first order of business; automation coming into further bolster processes and AI tying it all together with intelligent analysis. Along the way, continual iterations and feedback loops are critical to ensure solutions are adding value while still allowing for persistent innovation.
Giap Bui Dinh: We recommend using a “Fast to Mass” strategic framework to reach the maximum potential of these technology solutions. The strategy is rolled out in three stages that include task prioritisation, creating key performance indicators (KPIs) through surveys and developing resources for continuous deployment and application.